Principle, structure
The measurement principle of FE30H electromagnetic calorimeter is based on Faraday's law of electromagnetic induction: when a conductive liquid cuts magnetic field lines in a magnetic field, an induced potential is generated in the conductor, and the induced potential is E:
E=KBVD
In the formula: K - instrument constant
In the formula: B - Magnetic induction intensity
In the formula: V - the average flow velocity within the cross-section of the measuring tube
In the formula: D - measure the inner diameter of the pipeline cross-section
When measuring flow rate, a conductive liquid flows through a magnetic field perpendicular to the flow direction at a velocity of V. The flow of the conductive liquid induces a voltage proportional to the average flow velocity, and the induced voltage signal is detected by two or more induction electrodes in direct contact with the liquid and sent to a converter through a cable for intelligent processing, achieving the display of instantaneous fluid flow rate, accumulated flow rate, and communication between flow data and control system. There are no active or obstructed components inside the measuring tube, so there is almost no pressure loss and high reliability.
The electromagnetic heat meter combines an electromagnetic flowmeter and a paired temperature sensor organically. By using the electromagnetic flowmeter to measure flow and the paired temperature sensor (PT1000), it can calculate, accumulate, store, and display the heat absorbed or released in the heat exchange circuit. The flow and energy calculation unit CPU and sampling module of the FE30H electromagnetic heat meter are all equipped with ARM microcontrollers, which have large memory capacity and high reliability. The heat calculation can truly achieve enthalpy value calculation, achieving high accuracy.
Principles of Energy Measurement
The FE30H electromagnetic heat meter calculates and displays the heat released or absorbed by the system based on the flow signal from the flow sensor, the supply and return water temperature signal detected by the paired temperature sensor, and the time of water flow. The heat is displayed in the form of a meter, with a unit of KWh, a resolution of 1KWh, and a maximum display of 9 digits. The mathematical calculation model is as follows:

Structural appearance
Flange connection type

Threaded connection type
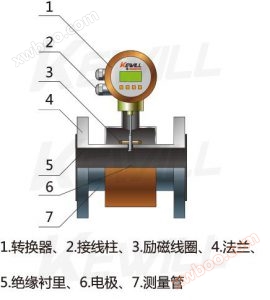
FE30H Electromagnetic Thermometer Features... Advantages
Electromagnetic calorimeter is an instrument for measuring volumetric flow rate, and the measurement results are independent of physical parameters such as flow velocity distribution, flow pressure, temperature, density, viscosity, etc
There are no moving parts inside the measuring tube, making it easy to maintain and manage, so the sensor has a long service life; No obstruction components, no pressure loss
The minimum conductivity of the tested liquid can reach 5 μ S/cm, and with various lining materials, it can be used to measure the flow rate of various acid and alkali media with high accuracy, usually with a flow rate accuracy of ± 0.5%
High definition backlit LCD display, Chinese English menu operation, easy to use, simple to operate, easy to learn and understand
The converter has reliable performance, high accuracy, low power consumption, stable zero point, convenient parameter setting, LCD display, and can display parameters such as cumulative flow rate, flow rate, and flow percentage
The water inlet direction can be bidirectional, and installation is not restricted. Bidirectional measurement system, capable of measuring forward flow and reverse flow
● All digital processing, strong anti-interference ability, reliable measurement, high accuracy, flow measurement range can reach 150:1
Ultra low EMI switching power supply, with a wide range of voltage variations and good EMC resistance
● Equipped with RS485 digital communication signal output
Can be applied to air conditioning, heating and circulation systems with generally poor water quality
It can display parameters such as cumulative heat, cumulative flow rate, instantaneous flow rate, flow rate, supply water temperature, and return water temperature.
● Correct with changes in water temperature to ensure accurate measurement at different water temperatures
● Multi level password setting function to prevent malicious modification of data
Technical Parameter
Nominal diameter (mm): | Pipeline type PTFE lining: DN10~DN800 | Flow rate range: | 0.3-12m/s | |||||
Pipeline type rubber lining: DN40~DN800 (special specifications can be customized) | Conductivity range: | The conductivity of the measured fluid is ≥ 5 μ s/cm | ||||||
Temperature difference range: | 2~75℃ | Current output: | load resistance | 4~20mA:0~750 KΩ | ||||
Temperature measurement range: | 4~95℃ | Power supply: | AC220V | |||||
Temperature resolution: | 0.01℃ | Total power consumption: | Less than 20W | |||||
accuracy: | 0.1℃ | Link method: | Flanges and threaded connections can be used between flow meters and piping | |||||
Temperature of the tested medium: | High temperature rubber lining: - 20~+90℃ | ambient humidity: | <90% r.h (non condensing) | |||||
Polytetrafluoroethylene lining: - 30~+100℃ | Protection level: | IP65 | ||||||
High temperature PTFE lining: - 20~+180℃ | Environmental temperature: | -25~+60 ℃ (please consult the engineer for special working conditions) | ||||||
Rated working pressure: (High pressure can be customized) | DN15-DN80:≤2.5MPa | Required length of straight pipe section: | Upstream ≥ 5DN, downstream ≥ 2DN | |||||
DN80-DN150:≤1.6MPa | Execution standards: | DIN EN 1092-1-2002 | ||||||
DN200-DN800:≤1.0MPa | Sales Usage Standard (Order Remarks) | |||||||
Display unit: | m³/H、m³/M、m³/S、L/H、L/M、L/S、G/H、G/M、G/S(H=Hour M=Minute S=Second) | LVD 2006/95/EC&EMC 2004/108/EC | ||||||
EN 61326-1:: 2006 Radiation Standard (BS EN50081-1) | ||||||||
EN 61326-1:: 2006 anti-interference standard (BS EN50082-1) | ||||||||
EN 61010-1: 2001 Equipment Safety Requirements: General Requirements |
Applicable Medium

installation drawing

application
Used for cold/heat metering in central air conditioning systems and heating metering in the heating market
Selection of Electromagnetic Thermometers
1. The correct selection of electromagnetic calorimeter requires a detailed understanding of the following process parameters:
Fluid name, composition, conductivity | Determine if an electromagnetic calorimeter can be used for measurement |
Fluid maximum temperature, minimum temperature, corrosiveness, wear resistance, and whether there is negative pressure | Determine whether an electromagnetic calorimeter can be used, what type of lining to choose, and electrode materials to use |
Pipeline inner and outer diameters (mm), common flow rate, normal flow rate, minimum flow rate | Determine which caliber of electromagnetic calorimeter to choose |
Maximum operating pressure and minimum operating pressure | Determine the pressure level of the calorimeter |
INSTALLATION REQUIREMENTS | Determine whether to choose a one-piece or split type structure, and the length of the split cable |
Installation environment | Determine the protection level of the calorimeter |
The actual maximum working pressure must be less than the rated working pressure of the electromagnetic calorimeter;
The minimum and maximum operating temperatures must comply with the temperature requirements specified in the flow measurement regulations (see the lining material table for details);
From an economic perspective, an electromagnetic thermal energy meter with a diameter corresponding to an appropriate flow rate can be selected to relatively reduce investment (see flow range table);
Reasonably select the corresponding accuracy level based on the measurement purpose and function;
Select electrode materials for electromagnetic thermometers based on the corrosiveness of the medium;
Select the lining material for the flow rate based on the corrosiveness, wear resistance, and temperature of the medium;
According to the requirements and environment of the installation site, choose whether to use an integrated electromagnetic thermal energy meter or a split type electromagnetic thermal energy meter reasonably.
2. Selection of Electromagnetic Thermometer Caliber:
Nominal diameter (mm) | Measurable flow range (m ³/h) | Nominal diameter (mm) | Measurable flow range (m ³/h) | ||||
minimum | maximum | in common use | minimum | maximum | in common use | ||
15 | 0.06 | 6.4 | 1.5 | 200 | 11.3 | 1130 | 250 |
20 | 0.11 | 11 | 2.5 | 250 | 17.66 | 1766 | 400 |
25 | 0.18 | 18 | 3.5 | 300 | 25.43 | 2543 | 600 |
32 | 0.29 | 29 | 6 | 350 | 34.62 | 3460 | 750 |
40 | 0.45 | 45 | 10 | 400 | 45.22 | 4522 | 900 |
50 | 0.71 | 71 | 15 | 450 | 57.23 | 5723 | 1200 |
65 | 1.19 | 119 | 25 | 500 | 70.65 | 7065 | 1500 |
80 | 1.81 | 181 | 40 | 600 | 101.74 | 10174 | 2500 |
100 | 2.83 | 283 | 60 | 700 | 138.47 | 13847 | 4000 |
125 | 4.42 | 442 | 100 | 800 | 180.86 | 18086 | 5000 |
150 | 6.36 | 636 | 150 |
3. Selection of lining:
Material type | Performance | scope of application |
neoprene | Good wear resistance, excellent elasticity, high tensile strength, and resistance to corrosion from low concentration acid-base salt media, but not resistant to corrosion from oxidizing media. | <90 ° C, general water, sewage, mud, slurry |
Polytetrafluoroethylene (PTFE) | The most stable material in terms of chemical properties, capable of withstanding boiling hydrochloric acid, sulfuric acid, nitric acid, aqua regia, concentrated alkali, and various organic solvents, but not resistant to chlorine trifluoride and high-temperature oxygen difluoride. | Strong corrosive media such as concentrated acid and alkali, sanitary media (PTFE lining: -30~+100 ℃; high-temperature PTFE lining: - 20~+180℃) |
4. Selection of electrode materials:
material | Corrosion Resistance |
316l stainless steel | Applicable: industrial water, domestic water, sewage, with a wide range of applications. |
Hastelloy HB | Resistant to all concentrations of non oxidizing acids, bases, and non chlorinated hydrochloric acids such as hydrochloric acid, sulfuric acid, hydrofluoric acid, and organic acids at boiling point. Not applicable: nitric acid |
Hastelloy HC | Resistant to oxidizing acids such as nitric acid, mixed acids, or mixtures of chromic acid and sulfuric acid, as well as oxidizing salts and seawater. Not applicable: Hydrochloric acid |
5. Selection of Thermal Energy Meter Types:
Split type
Split type is a common application form of electromagnetic thermal energy calculation. The sensor is separately connected to the process pipeline, and the converter is installed in other places several meters or more apart, connected by cables in between. A split type calorimeter can keep the converter away from harsh environments and facilitate observation and adjustment of set parameters.
All-In-One
One in one type refers to the assembly of a converter and a sensor into a whole, with the connecting wires inside the instrument. It is relatively easy to use, and due to the infrequent use of cables, external interference is also relatively small. Integrated flow meters are generally used for small caliber instruments. If the sensor is installed at a high place or in difficult to observe environments, such as high temperatures or large vibrations, and the electronic components of the converter are difficult to withstand, integrated electromagnetic thermometers should not be used.
6. Selection of grounding ring:
(1) The forms of grounding rings are divided into universal and protective types. Generally, universal type is used. If the tested medium is abrasive, a protective grounding ring with a neck should be used to protect the lining at the inlet and outlet ends and extend the service life. If the diameter of the electromagnetic flowmeter is below 200, when using a polytetrafluoroethylene lining, a grounding ring should be selected to ensure that the lining is not damaged during installation and connection with the pipeline.
(2) The material of the grounding ring should be compatible with the corrosiveness of the tested medium, but with lower requirements than the electrode material, as it can be replaced after corrosion. The grounding ring is usually made of stainless steel or Hc alloy.
7. Selection of Protection Level for Electromagnetic Thermometers:
IP65: Dustproof and water-resistant type | Allow the faucet to spray water onto the sensor from any direction, with a spray pressure of 30KPa and a water output of 12.5L/min. Distance is 3m |
IP67: Dustproof and waterproof type | Prevent short-term water intrusion. After about 30 minutes of immersion in 1 meter of water, the amount of water intrusion into the shell should not reach a harmful level |
IP68: Dustproof and anti diving type | Sensors work in water for a long time |
8. Selection of Special Voltage Resistance for Electromagnetic Thermometers:
The pressure resistance of sensors is related to their inner diameter. According to the relevant national standards and regulations for product application, the maximum pressure resistance of standard steel pipes and flanges is as follows:
caliber | pressure resistance |
DN-10~80 | 4.0MPa |
DN-100~150 | 1.6MPa |
DN-200~800 | 1.0MPa |
Note: If the pressure of the fluid inside the sensor exceeds the maximum pressure resistance mentioned above, it belongs to the pressurized type and requires special customization
2. Except for sensors lined with polytetrafluoroethylene, sensors lined with other materials can operate under negative pressure in pipelines
Dimensional drawing (flange type)
Flange type dimension diagram
Integrated split type
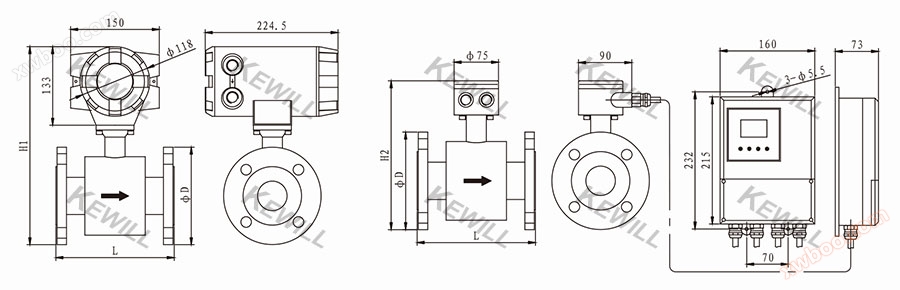
Size (mm) | Dimensions between flange sections L (mm) | Outer diameter of flange D (mm) | Height H1 (mm) | Height H2 (mm) | |||||||||||||
PTFE lining | rubber lining | ||||||||||||||||
15 | – | – | 95 | 277 | 214 | ||||||||||||
20 | – | – | 105 | 284 | 221 | ||||||||||||
25 | 156 | – | 115 | 293 | 230 | ||||||||||||
32 | 156 | – | 140 | 304 | 241 | ||||||||||||
40 | 196 | – | 150 | 317 | 254 | ||||||||||||
50 | 196 | – | 165 | 331 | 268 | ||||||||||||
65 | 200 | 200 | 185 | 348 | 285 | ||||||||||||
80 | 200 | 200 | 200 | 363 | 300 | ||||||||||||
100 | 250 | 250 | 220 | 382 | 319 | ||||||||||||
125 | 250 | 250 | 250 | 414 | 351 | ||||||||||||
150 | 300 | 300 | 285 | 445 | 382 | ||||||||||||
200 | 350 | 350 | 340 | 506 | 443 | ||||||||||||
250 | 400 | 400 | 395 | 559 | 496 | ||||||||||||
300 | 500 | 500 | 445 | 609 | 546 | ||||||||||||
350 | 500 | 500 | 505 | 645 | 582 | ||||||||||||
400 | 600 | 600 | 565 | 698 | 635 | ||||||||||||
450 | 600 | 600 | 615 | 748 | 685 | ||||||||||||
500 | 600 | 600 | 670 | 803 | 740 | ||||||||||||
600 | 600 | 600 | 780 | 910 | 847 | ||||||||||||
700 | 700 | 700 | 895 | 1046 | 983 | ||||||||||||
800 | 800 | 800 | 1010 | 1154 | 1091 |
Dimensional drawing of threaded connection type

Size (mm) | Body face size | Outer diameter D | H1(mm) | thread specification | |||
L(mm) | |||||||
15 | 160 | 89 | 272 | G1 | |||
20 | 160 | 89 | 272 | G1 | |||
25 | 160 | 89 | 272 | G1-1/4 | |||
32 | 160 | 89 | 272 | G1-1/2 | |||
40 | 160 | 102 | 285 | G2 | |||
50 | 160 | 108 | 291 | G2-1/2 |
FE30H Installation Requirements
Requirements for upstream and downstream straight pipe sections of sensors:
In order to ensure the accuracy stated in the manual under different application conditions, a straight pipe section with a diameter five times the diameter should be installed upstream of the electrode surface and a straight pipe section with a diameter three times the diameter should be installed downstream when installing the sensor, as shown in the following figure. This installation can fully eliminate interference caused by bends, valves, or necking. When the straight pipe sections before and after the flowmeter cannot meet the requirements, there will be a certain deviation in performance indicators.
Grounding requirements for sensors:
There must be a reliable grounding path between the electromagnetic calorimeter sensor and the measured medium. There are three grounding methods to choose from: grounding electrode, grounding ring, and pipeline grounding. Please refer to the selection table for details.

Model Selection Table
FE30H- | Electromagnetic thermal energy meter (cold energy meter) | ||||||||||
Installation type of transmitter | |||||||||||
Integrated on-site display setting type | |||||||||||
Split remote transmission display setting type (square) | |||||||||||
orifice | |||||||||||
15 to 800mm (such as pipe diameter DN15 and expressed as 15) | |||||||||||
Installation method | |||||||||||
Threaded type (DN15 to DN50) | |||||||||||
Flange type (DN15 to DN800) | |||||||||||
Electrode material | |||||||||||
Electrode Material Stainless Steel 1.4435 (316L) | |||||||||||
Electrode material Hastelloy HC | |||||||||||
Electrode material Hastelloy HB | |||||||||||
Shell and flange material | |||||||||||
Main material: Carbon steel | |||||||||||
Main material: Stainless steel 1.4301 (304) | |||||||||||
Main material: Stainless steel 1.4435 (316L) | |||||||||||
Output | |||||||||||
no-output | |||||||||||
4 to 20mA+pulse | |||||||||||
Lining material | |||||||||||
Inner lining material PTFE (polytetrafluoroethylene) | |||||||||||
Lining Material PUR (Polychloroprene Rubber) | |||||||||||
Power supply mode | |||||||||||
AC 85V to 265V | |||||||||||
DC 24V | |||||||||||
accuracy class | |||||||||||
1% | |||||||||||
2% | |||||||||||
(Optional accessory) Grounding method | |||||||||||
No grounding ring | |||||||||||
Stainless steel 1.4435 (316L) grounding ring | |||||||||||
Titanium alloy grounding ring | |||||||||||
The above selection table does not include selection codes. If you need selection codes, please contact us or fill in your information |
Process connection withstand voltage level | /D6 | EN 1092-1(DIN) PN6 | |||||
/D10 | EN 1092-1(DIN) PN10 | ||||||
/D16 | EN 1092-1(DIN) PN16 | ||||||
/D25 | EN 1092-1(DIN) PN25 | ||||||
/D40 | EN 1092-1(DIN) PN40 | ||||||
/D63 | EN 1092-1(DIN) PN63 | ||||||
/D100 | EN 1092-1(DIN) PN100 | ||||||
/D250 | EN 1092-1(DIN) PN250 | ||||||
/P | Special standards for product application areas |
Alternative options: Interface standards&communication methods | /2 | Communication: RS485 |